Денис Прудников, К2Тех Себестоимость продукта можно снизить на 10% за счет внедрения MES-системы
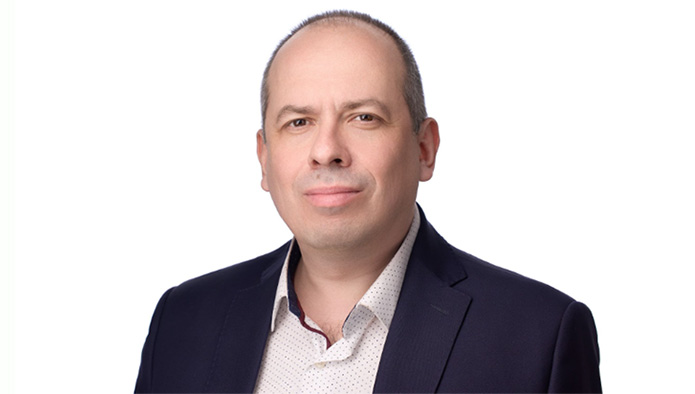
Более 90% рынка систем оперативного управления производством занимали западные вендоры, которые покинули России. На этом фоне на рынке появилось множество разработчиков, предлагающих различные альтернативные решения. В чем их основная проблема, какие риски имеет предприятие при работе с такими командами и почему интегратору К2Тех пришлось разрабатывать собственный продукт для оперативного управления производством, рассказывает эксперт по решениям для цифрового производства Денис Прудников.
Milknews: Как вы оцениваете уровень автоматизации управления производством на российских молокоперерабатывающих предприятиях сегодня?
Д. Прудников: Полноценное внедрение MES-систем завершено, по нашим оценкам, примерно у 20-25% молочных предприятий. В основном это крупные западные холдинги, российская часть которых осталась работать на отечественном рынке. На российских заводах уровень автоматизации управления производством зачастую не такой высокий. Для составления производственных планов используются электронные таблицы, данные о выпуске продукции, потреблении сырья и материалов собираются вручную и хранятся в разных местах и форматах. Как следствие – много ошибок, расхождения в план-фактах, увеличение себестоимости продукции. Конечно, развивать бизнес на базе такого производственного процесса очень сложно. И мы видим, что многие предприятия сегодня приходят к выводу, что нужно автоматизировать управление производством.
Milknews: Что изменилось на рынке за последний год? Какие сегодня системы доступны для внедрения?
Д. Прудников: После ухода западных компаний, которые были основными поставщиками IT-решений для пищевой индустрии, в России стали активно появляться свои команды, которые представили свои разработки. Но проблема этих продуктов в том, что их внедрением и поддержкой может заниматься только команда разработчика, поскольку решения слабо документированы, зачастую отсутствуют стандартные механизмы доработки систем сторонними командами. В этом случае работоспособность решения у заказчика полностью зависит от единственного разработчика. Для нас как для интегратора такая ситуация на рынке стала серьезным вызовом. Поэтому мы разработали собственный продукт – систему оперативного управления производством РеMESло. Она ориентирована прежде всего на предприятия, выпускающие молочную продукцию и другие напитки. Решение состоит из четырех модулей разного назначения: хранение нормативно-справочной информации, план-фактный анализ, управление оборудованием и контроль эффективности производства, контроль и аналитика CIP-процессов. Поскольку мы много занимались поддержкой и внедрением MES-систем, то хорошо понимали, как такое решение должно быть реализовано, в том числе для внедрения и поддержки сторонними силами. Мы создали набор модулей, описали и задокументировали их для внедрения, открыли и описали интерфейсы для доработки, создали интеграционную платформу.
Milknews: Насколько сложный для бизнеса процесс внедрения MES-систем?
Д. Прудников: Внедрение MES – процесс, который затрагивает как техническую, так и организационную сторону производства. Интегратору иногда приходится подстраивать систему под конкретное предприятие, а предприятию – изменять сами принципы управления производством. Но, при использовании четкой методологии, данный процесс проходит для предприятия безболезненно. Одна из главных задач связана с подготовительным этапом, который предполагает оценку того, что предстоит сделать. В нашей практике много подобных проектов и во всех случаях мы сначала проводим аудит, моделируем и обсуждаем с заказчиком будущие производственные процессы, даем бюджетную оценку. И обязательно прописываем шаги, которые нужно сделать, чтобы решение заработало на конкретном предприятии. С внедрением MES-систем производство из «черного ящика» превращается в прозрачный механизм с четкими и формализованными процессами. И к этому предприятие должно быть готово на всех уровнях производственного процесса.
Milknews: Как РеMESло интегрируется с другими системами?
Д. Прудников: Как и любая система, наш продукт не работает в технологическом вакууме. Поэтому мы предусмотрели механизм его интеграции как с производственными системами, так и со смежными корпоративными системами, такими, как, например, ERP. И, конечно, мы понимаем, что на многих предприятиях используются различные самописные решения, которые могут вполне устраивать заказчика. И в этом случае мы просто интегрируем ее в РеMESло. Если же предприятие хочет уйти от самописных решений, тогда мы замещаем их модулями нашей системы.
Milknews: Есть ли уже реализованные кейсы? Какой результат?
Д. Прудников: Недавно мы завершили внедрение системы РеMESло на нескольких заводах одного из крупнейших молокоперерабатывающих предприятий России. Этот проект ярко иллюстрируют то, о чем я говорил ранее: прежде всего компания должна пересмотреть свою производственную модель, быть готовой к изменениям. Когда мы начали проводить аудит на предприятии, не было даже нормативно-справочной информации. Никто не понимал, сколько времени должна занимать та или иная операция. Все нормы формировались по ходу проекта, заказчик собирал статистику, мы моделировали эти данные на работу в MES-системе, и так появились маршрутные карты.
После внедрения системы РеMESло специалисты по производству на всех заводах холдинга стали формировать планы производства в единой информационной среде и отслеживать его соблюдение в режиме, близком к реальному времени. Нормативно-справочная информация – рецептуры, маршрутные карты предприятия, – теперь хранятся в единой системе и управляются из нее. Вся информация о производстве автоматически передается в корпоративные системы – это позволяет бизнесу оперативно принимать управленческие решения.
Внедрение системы решило еще одну важную для заказчика задачу – контроль процесса технологических моек. Для этого в системе РеMESло существует модуль CIP-аналитики, который собирает данные с оборудования, сравнивает их с эталонными сценариями и строит диаграммы с деталями мойки. По ним можно увидеть фактический состав и концентрацию моющих средств, расход газа, воды, пара и другие параметры. В ходе аналитики заказчик обнаружил перерасход одного из энергоресурсов из-за неисправности датчика и нарушения целостности трубопровода, благодаря чему в последующем потребление этого ресурса удалось сократить на 30%.
По отчетам заказчика, оптимизация затрат на производство после внедрения системы помогла снизить себестоимость продукции на 10%.
Примеры интерфейса системы оперативного управления производством РеMESло
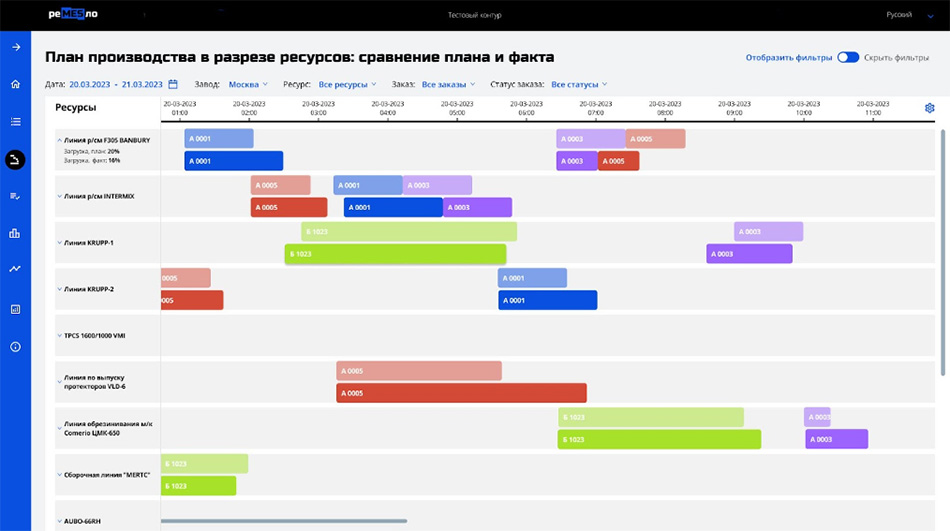
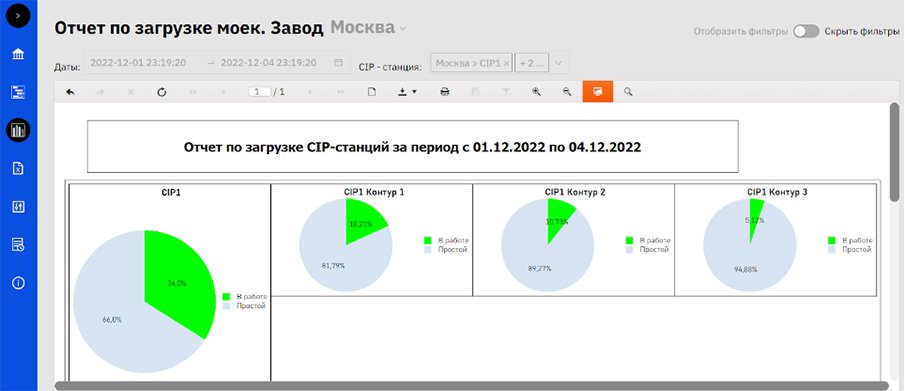
Milknews: Какие планы дальнейшего развития продукта?
Д. Прудников: В ближайших планах - разработать и интегрировать в решение блок оперативного планирования производства, который позволит свести к минимуму переходы и переналадки и уменьшить незавершенное производство. Также мы хотим добавить модуль полной прослеживаемости производства, который собирает полные данные о производстве на каждом рабочем центре и обеспечивает полную “прозрачность” исполнения любого производственного заказа – от приемки сырья и материалов до отгрузки готовой продукции. Мы постоянно собираем обратную связь от заказчиков, анализируем потребности рынка, поэтому наша система будет дорабатываться и расширять свой функционал в соответствии с запросами предприятий.
Сегодня, когда на рынке снижается покупательская способность, а конкурировать в ценовом поле становится все сложнее, все владельцы предприятий понимают, что нужно повышать эффективность управления предприятием. Только нормальная система оперативного управления производством, которая позволяет вести четкое планирование производства, управлять оборудованием, снижать объем ручного труда и минимизировать ошибки из-за человеческого фактора, оценивать общую эффективность производственных процессов позволит компании расти дальше и открывать новые горизонты, в том числе экспортные.